GDI
Injector Information
To meet customer demands for cheaper prices, better performance and
greater
fuel economy, vehicle manufacturers are
all switching to Direct Fuel Injection. Be it for diesel or
petrol fuel, Direct Injection is the only way forward.
The abbreviation GDI (with a capitalised letter "I") is a
registered trademark of Mitsubishi Motors. Other companies
have developed other names for what is Gasoline Direct
Injection (GDI) engines but have had to change their brand
name of their system, VW/Audi have branded their system
(Fuel Stratified Injection) Alfa Romeo — JTS, Renault — HPI
and so on, the fact is they are all Gasoline fuel fired
directly into the combustion chamber.
On a direct injection engine, a very fine mist of fuel is
injected directly in to the combustion chamber at a pressure
of between 50 — 120 Bar, depending on the type of system.
During idle and light throttle, the metered fuel is injected
at microscopic milli-second (mS) durations at a pressure of
approximately 50 bar.
This design enables the engine to operate a stratified
charge combustion, described by most of the vehicle
manufacturers as an Ultra Lean Burn mode, giving a much
improved fuel efficiency, great engine torque and reduced
Exhaust Emission levels at low load. To achieve these
pressures, the gasoline is pressurized by a high-pressure
pump that is a combination of mechanically driven and
Electronically controlled and mounted on the engine. This
pump compresses the fuel to the pressure level required in
fuel rail
With the sequential firing GDI systems, the injector only
opens to a maximum of 5mS. As the fuel requirement
increases, the injector remains at 5mS and the pump pressure
increases to meet the demand, allowing the injector to open
and close quickly and efficiently. No more "Duty Cycle" as
we have known it. These engines use a very high
specification injector, Hitachi, Bosch, Denso and Siemens
being the major suppliers.
The ASNU GDI Adapter Box has been designed to drive Gasoline
Direct Injection (GDI) injectors with an approved supply of
current and voltage to simulate injector electronic
operation as on the engine. Correct Electronic Operation is
critical when examining the injector's response to changes
in mS & RPM. Examination of the injectors Fuel Distribution
and Atomisation is equally critical to the Engine's Correct
Running, Performance, Fuel Economy and Emission Outputs.
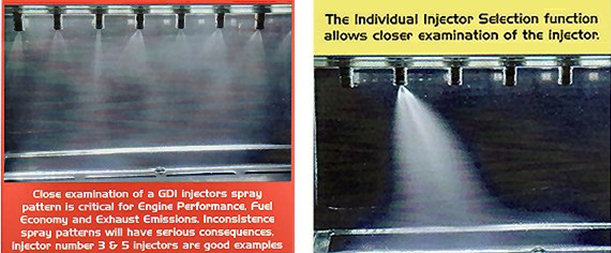
Carbon can build up on the tip of the injector and interfere
with the distribution and atomisation of the fuel. Even the
slightest loss of the fuel delivery will have an adverse
effect on the engines Drivability, Power Output, Fuel
Economy and Exhaust Emissions. This style of injector can
have varying types of spray patterns, depending on the
engine requirements, but all of them will be atomising a
much smaller fuel droplet size. To explain the difference, a
conventional injector would have a fuel droplet size, as an
example, of 165 micron, some GDI injectors would produce a
fuel droplet of say, only 65 micron.
The ASNU GDI Adapter Box is designed to work with all
currently produced injectors. To enable the user to analyze
the fuel spray pattern easier and measure the fuel flow rate
more accurately The GDI Adapter Box has a specific range of
settings that will enable the user to check the injectors
electronic operation, clearly see the injectors spray
pattern form and accurately measure the injector delivery
flow rates.
These systems use a much smaller duration of opening time
and fuel metering supply. To enable the injectors to operate
and respond to these demands, they must receive a greater
power supply and the injectors are of a much higher standard
of those used in a conventional injection system. Even the
slightest irregularity in the Fuel Spray pattern would
result in illumination of the Engine © Check Light, but with
no specific cause identified. GDI injectors are difficult
and time consuming to remove and re-fit, would you fit a set
of injectors without ensuring they are working correctly?
Text courtesy ASNU